The 6-Second Trick For Indonesia Furniture Manufacturers
The 6-Second Trick For Indonesia Furniture Manufacturers
Blog Article
The Only Guide for Indonesia Furniture Manufacturers
Table of ContentsThe Ultimate Guide To Indonesia Furniture ManufacturersExcitement About Indonesia Furniture ManufacturersExcitement About Indonesia Furniture ManufacturersThe 25-Second Trick For Indonesia Furniture ManufacturersHow Indonesia Furniture Manufacturers can Save You Time, Stress, and Money.
There are some disadvantages to buying from a furniture maker. A furnishings seller is a business that sells furniture made by different makers.When you purchase from a furniture store, you're getting a piece of furnishings that's currently been made and prepares to be delivered to your home. Among the advantages of purchasing from a furniture seller is that you can usually see and touch the product prior to you get it.
At BH Furniture, we believe in establishing brand-new criteria for quality in the manufacturing of business furniture - Indonesia furniture manufacturers. Our commitment to advancement has led us to welcome innovative automation modern technology, transforming the method we make furnishings and propelling us to the leading edge of the industry. Gone are the days of manual work dominating the production floor
Claim bye-bye to manufacturing hold-ups and overtime prices. This suggests we not only meet yet surpass distribution due dates, supplying our clients with a degree of dependability that typical manufacturing approaches merely can't match.
The Basic Principles Of Indonesia Furniture Manufacturers
Our production capacity has actually skyrocketed, allowing us to meet the demands of even the biggest tasks without compromising on quality. As your partner in business furnishings options, we can easily scale our output to suit your requirements, no issue the range. While conventional production relies greatly on manual labor, our automated systems have significantly reduced our dependence on a big workforce.
Furnishings manufacturing is a complex procedure that entails various phases, from developing and product choice to manufacturing and setting up. At each phase, there is an opportunity of flaws or mistakes that can jeopardize the high quality of the final product. To guarantee that furniture is of top quality, furnishings suppliers apply high quality control processes to recognize and remedy any kind of issues that may emerge throughout manufacturing.
The evaluation process ought to cover numerous elements, such as assembly, coating, colour, style, packaging, labelling, and noting. By implementing an extensive examination process, manufacturers can ensure their items meet the necessary high quality, safety and security, and toughness demands. They also supply the flexibility to address issues and make improvements prior to completing the final product.
Furnishings high quality requirements are collections of guidelines and demands for furniture manufacturing. next They define the needed quality degree of furniture manufacturing and cover elements such as security, toughness, stamina, and environmental effect.
Getting The Indonesia Furniture Manufacturers To Work

To guarantee their furniture items can sustain different weather elements, including sunlight, rainfall, snow, and wind, makers should take into consideration worldwide identified criteria that consist of inspections and screening. check here Right here are several of the requirements to bear in mind: ASTM F1561-03 is a worldwide standard developed by the American Section of the International Association for Testing Products (ASTM).
UL 962 is a global safety and security standard established by Underwriters Laboratories (UL), an independent international supply safety solutions firm. The standard applies to home and commercial furnishings, consisting of outdoor furnishings.
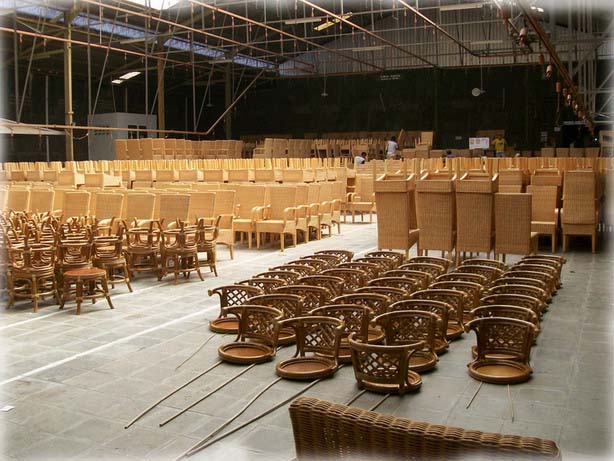
The 3-Minute Rule for Indonesia Furniture Manufacturers
It assists to determine issues in the furniture and evaluate its performance and compliance with the called for quality criteria. Here are the steps for conducting laboratory screening for furniture: Producers accumulate examples of furnishings parts that need screening. These samples usually stand for the various kinds of furniture that they produce.
This might involve a mix of various tests, including strength testing, durability screening, safety testing, and environmental influence testing. The examples are after that examined for various quality specifications, such as stamina, longevity, safety, and ecological effect. The outcomes are then assessed to establish whether the products meet the required high quality standards.
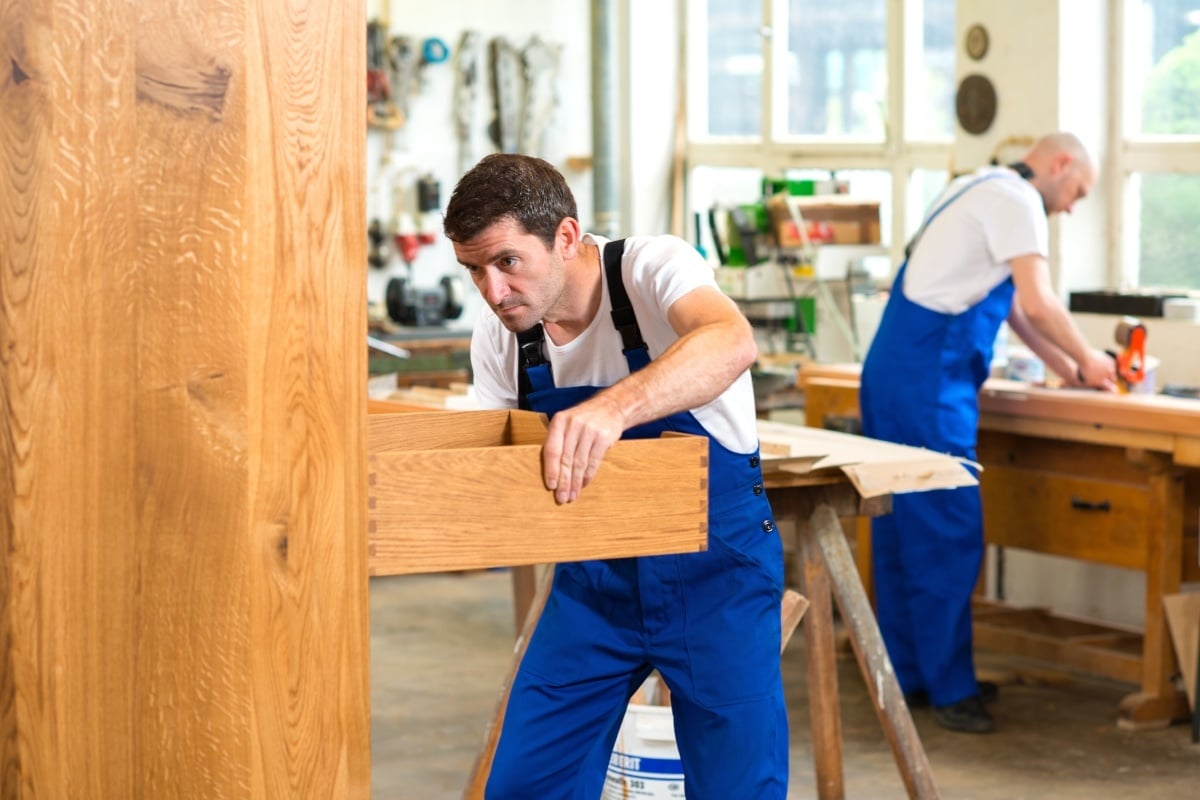
Typically, every retail store furniture is various. Layouts conference client convenience Making the most of space usage in storage space, screen, tramp, visitor seats and sidewalks Bonuses Ensuring convenience of access to products for tests and acquisition Creating modular furnishings that is easy to relocate and renovate Satisfying safety demands of consumers A quick TAT from design to production and installment with marginal errors can help address the above worries.
Some Known Facts About Indonesia Furniture Manufacturers.
Also, a designer can understand the marketplace patterns and be all set with innovative styles in advance. Check out below: Exactly How DriveWorks Assists You to Reduce Lead Time in Production Designers usually have to alter the shapes and sizes of furniture at a moment's notification. These may have various aesthetic and practical demands like front desk, and servicing desk that differ in dimensions.
Enhances item top quality and reduces scrap. Area direction documents along with quantity takeoffs are additionally created for retail store furniture installations. Style iterations and conflicts are reduced, and the shop floor can start producing on the day of sales.
It is a very affordable market, with services making every effort to keep up with changing customer needs and the newest technological fads. Today's consumers are much more likely to favor furniture that is customized and made with lasting materials.
Report this page